What is a Mineral Processing Plant?
Introduction to Mineral Processing Plant
Mineral processing plant is industrial facilities dedicated to the extraction and production of useful mineral resources found in mined ores. They utilize physical and chemical treatment methods to separate valuable minerals from waste gangue materials and produce high-purity products for further refinement into metals, ceramics, construction materials and more. By optimizing comminution, concentration and dewatering steps, mineral processing plants efficiently add value to mined ores for a multitude of end markets worldwide.
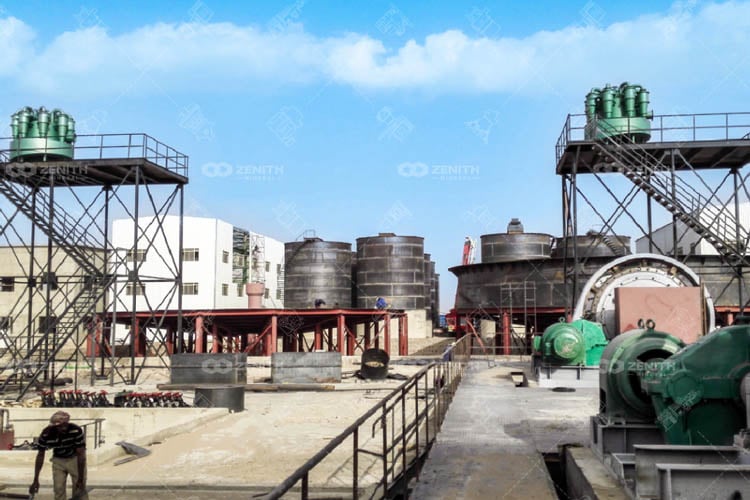
The Importance of Mineral Processing
Mineral processing is essential for several reasons:
- Resource Recovery: Efficient processing maximizes the extraction of valuable minerals, ensuring that resources are utilized effectively.
- Sustainability: By recycling and reusing materials, mineral processing contributes to sustainable practices in mining and manufacturing.
- Economic Value: High-quality processed minerals can command better prices in the market, enhancing the economic viability of mining operations.
Four Stages of Mineral Processing Plant
A typical mineral processing plant consists of comminution, screening, concentration, and dewatering. stages to liberate, concentrate and prepare marketable concentrates from mined ores. Crushing and grinding (comminution) reduce ore particle size for further processing. Screening separates stone sizes while classification separates minerals by shape differences. Concentration enriches target minerals from gangue using gravity, flotation or magnetic separation. Dewatering removes excess moisture from concentrates ahead of transport or further processing. Plant configuration varies depending on mineralogy, feed material and targeted product characteristics.
1. Comminution
Comminution is the first step in mineral processing, involving both crushing and grinding. The purpose is to break down large pieces of ore into smaller fragments, making it easier to extract valuable minerals.
- Crushing: This process reduces the size of ore using various types of crushers, such as jaw crushers, cone crushers, and impact crushers. Each type has its specific applications depending on the hardness and type of ore.
- Grinding: After crushing, the ore is further ground to achieve the desired particle size. Grinding equipment includes ball mills, rod mills, and autogenous mills, each suited to different types of materials and processing requirements.
2. Sizing/Screening
Sizing, or screening, involves separating ore particles based on size. This step is crucial for ensuring that the material is processed effectively in subsequent stages.
- Screening Methods: Common methods include vibrating screens and trommel screens, which classify particles by size as they pass through various screens.
3. Concentration
Concentration is the core step in mineral processing, aimed at separating valuable minerals from waste rock or gangue. Several techniques are employed:
- Gravity Separation: This method relies on differences in specific gravity to separate heavier minerals from lighter ones. It is effective for minerals like gold, tin, and tungsten.
- Froth Flotation: A widely used technique that separates minerals based on their ability to attach to air bubbles. It is particularly effective for copper, lead, and zinc ores.
- Magnetic Separation: This method utilizes differences in magnetic properties to separate magnetic minerals from non-magnetic ones, commonly used for iron and titanium ores.
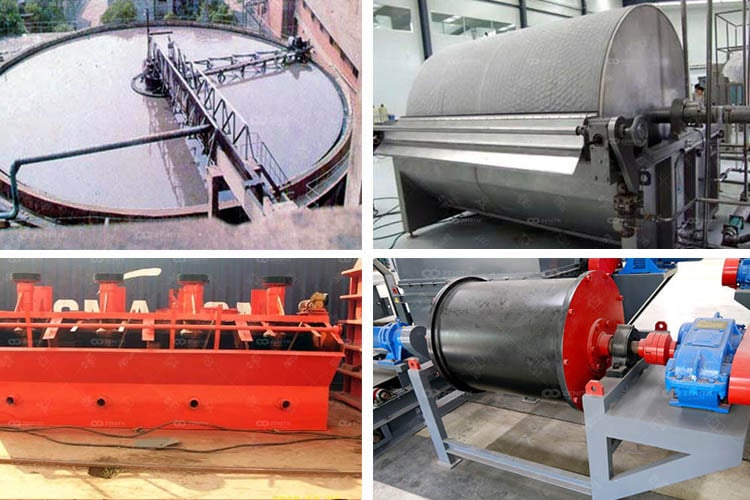
4. Dewatering
Dewatering is essential for preparing the processed ore for further handling and transport. Beneficiated concentrates typically contain high moisture levels, which must be reduced through various methods, including:
- Filtration: Removes moisture from concentrates to achieve a desired level of dryness.
- Drying: Techniques such as rotary drum drying and airflow drying are employed to reduce moisture content effectively.
Plant Objectives
The main objectives of mineral processing plants are to:
- Maximize liberation of target minerals from waste gangue for effective concentration.
- Achieve high mineral recovery rates with production of commercial grade/quality concentrates.
- Meet specific size and purity requirements for end user applications.
- Minimize water, energy and reagent consumption through efficient process control.
- Ensure environmental compliance through containment, recycling and residue/effluent management.
- Maintain operational safety and reliability with proper equipment/infrastructure design.
Equipment Used in Mineral Processing Plants
Mineral processing plants rely on a variety of specialized equipment to carry out the necessary processes. Understanding the function and application of each type of equipment is crucial for efficient plant operation.
1. Crushing Equipment
Crushing forms the preparatory comminution stage, reducing size for further grinding/concentration. The most common crushing equipment includes:
- Jaw Crushers: Heavy-duty units handle coarse primary crushing of run-of-mine ore down to 150mm or finer. Reversible swing motion compresses feed against fixed plate.
- Cone Crushers:Ideal secondary/tertiary machines provide fine/medium crushing, using rotating bowl eccentric motion against concave mantle to refine sizes below 50mm.
- Impact Crushers: Suitable for soft to medium-hard materials, impact crushers utilize high-speed hammers or blow bars for particle impact fracture. Output below 10-20mm.
- Mobile Crushers: Self-propelled modules provide crushing services directly at extraction faces. Variable configurations suit any secondary or tertiary crushing role.
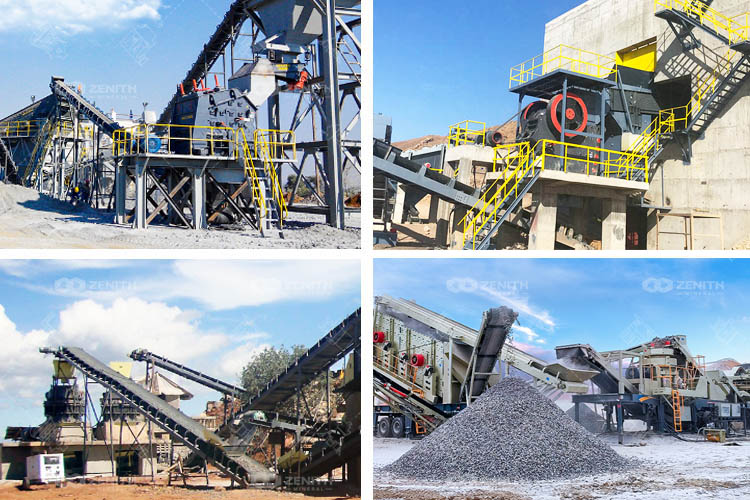
2. Grinding Plant Equipment
Comminution continues at finer levels through size-reduction mills, exposing valuable mineral grains. Common grinding equipment:
- Ball Mills: Large revolving cylinders contain grinding media like steel/ceramic balls. Batch/continuous wet/dry mills grind to sub-micron levels.
- Rod Mills: Rod mills drive long steel rods against ore for coarse grinding tasks. Effective for large feed particle sizes.
- SAG Mills: SAG mills rely on tumbling ore itself for comminution. Suitable for initial grinding of hard, abrasive ores.
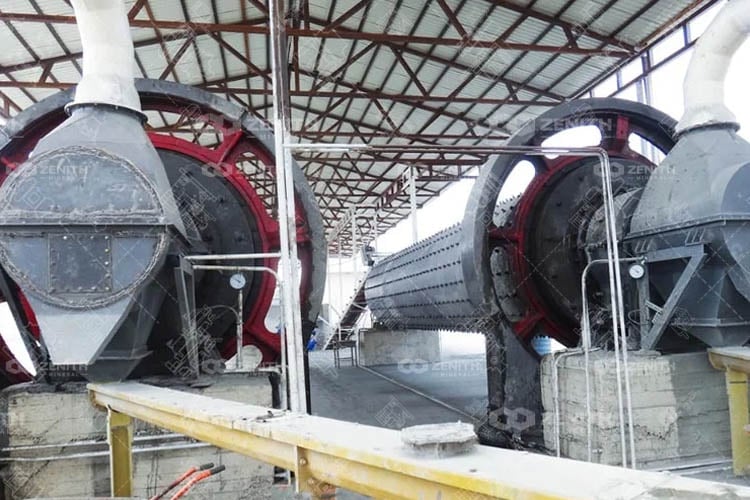
3. Mining Equipment
The core of a mineral processing plant consists of equipment designed to separate minerals through various methods:
- Flotation Machines: Separate minerals by utilizing mechanical agitation and bubble buoyancy.
- Magnetic Separators: Available in dry and wet types, they are essential for mineral separation based on magnetic properties.
- Shaking Tables: Utilize vibrations and water flow to separate minerals by density, particularly effective for fine metal minerals.
- Spirals/Jigs: Gravity devices concentrate dense minerals in water using laminar flow principles.
- Thickeners/Filters/Centrifuges: Remove tailings liquor to produce saleable concentrates for shipment or further valorization.
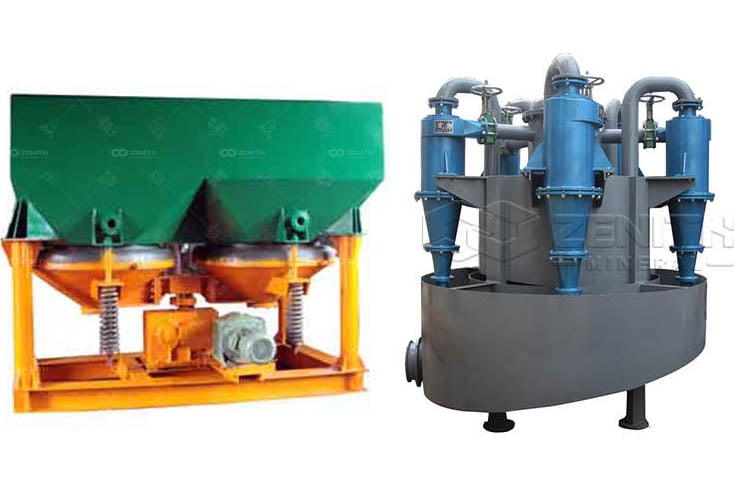
4. Screening Equipment
Screening equipment classifies ore particles to ensure efficient processing:
- Vibrating Screens: High-frequency vibrations separate particles by size, essential for grading final products.
5. Drying Equipment
Drying equipment is vital for reducing moisture content in concentrates:
- Rotary Drum Dryers: Commonly used for drying mineral concentrates and other materials.
- Airflow Dryers: Effective for materials requiring moisture control.
6. Auxiliary Equipment
Auxiliary equipment supports the overall processing operation:
- Feeders: Such as vibrating feeders, which ensure continuous and even feeding of ore into crushing or grinding equipment.
- Conveyor Belts: Transport ore and concentrates between processing stages, maintaining a continuous flow of materials.
Mineral Processing Plant Design Considerations
Evaluating process design alternatives requires assessing:
- Ore mineralogy/composition: effects liberation, separation techniques.
- Feed material characteristics: hardness, moisture content, contaminants.
- Process flowsheet: unit operations, material flow, equipment.
- Water availability: process/dust control needs, tailings disposal.
- Energy/reagent costs: comminution power, concentration chemicals.
- Capital/operating expenditures: infrastructure, machinery, labor.
- Environmental permitting: waste management, emissions/spills control.
- Production targets: capacity, recovery rates, quality specifications.
Rigorous testing aids optimal design selections balancing recoveries, costs and sustainability for maximum long-term value.
Mineral processing plants are vital to the mining industry, providing the necessary infrastructure to transform raw ores into valuable products. Through a series of complex processes involving comminution, sizing, concentration, and dewatering, these plants ensure optimal recovery and product quality. As the industry continues to evolve, the integration of advanced technologies and sustainable practices will play a crucial role in shaping the future of mineral processing.